Benefits of Hydrostatic Liquid Level Sensing Technology
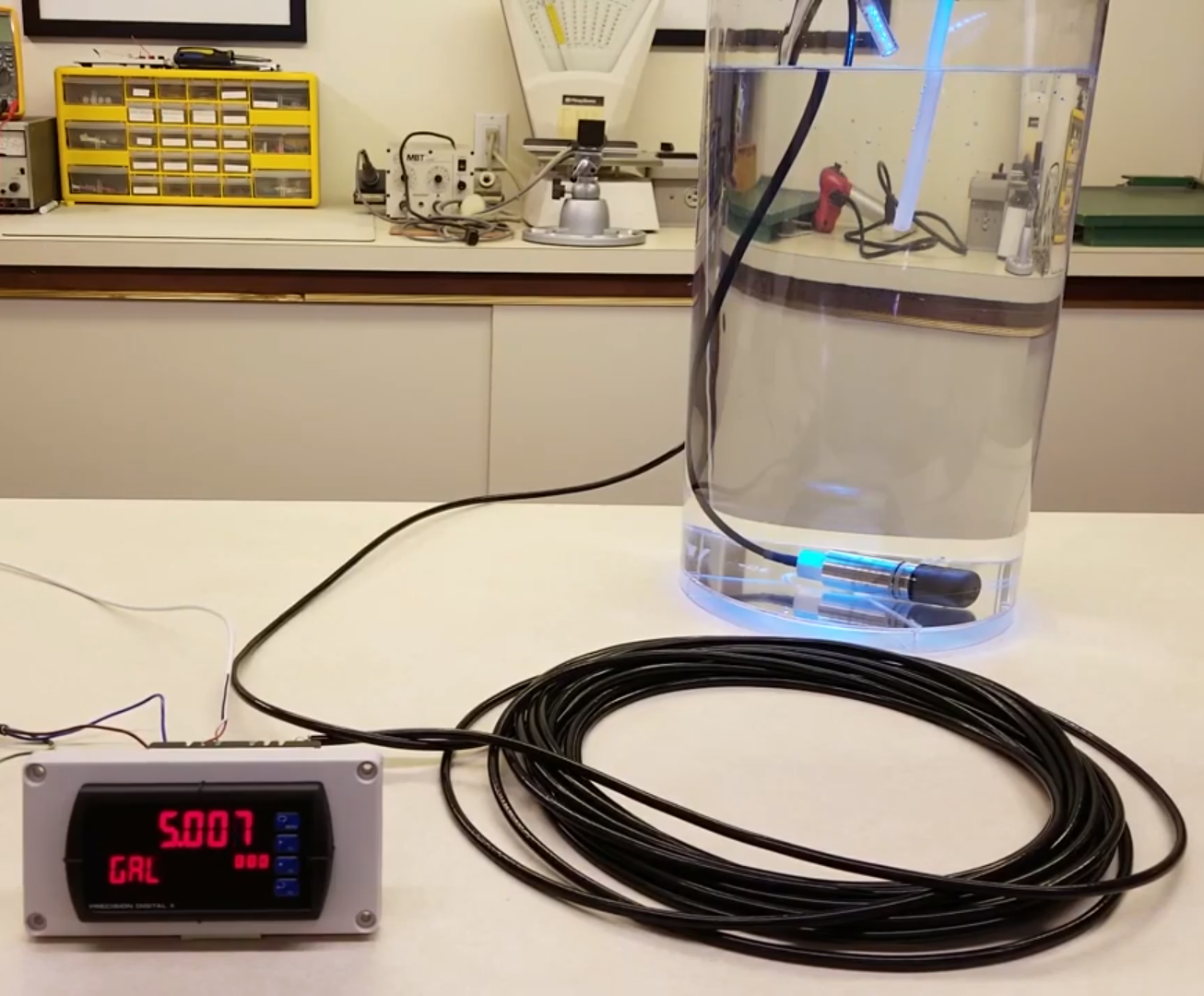
The Situation
Liquid level sensing is a tremendously important engineering challenge that is critical in many industries around the world, from factories to municipal water systems. Though technology has made progress in leaps and bounds in recent years, many traditional technologies are still widely used for a plethora of possible reasons, even on new systems. For example, one may be simply maintaining or repairing an old system because it seems quicker or less costly, it may be what the engineers are familiar with, parts may still be on hand, or maybe it “just works.” However, there are many important reasons to consider newer technologies, such as hydrostatic level sensing.
The Problem
Implementing and maintaining liquid level control systems can be complex, and varies significantly depending on the installation. Therefore, many common challenges come along with it. For example, different types of liquids can require vastly different types of systems. Even slight differences in mineral content or length of probe leads can present challenges for traditional technologies. Furthermore, once many types of systems are in place, they are difficult to work on and potentially require significant overhaul for even small tweaks like changing a pump set point. Even more importantly, their capabilities are significantly more limited with regards to important features such as alarms or multiple-pump control. Finally, many such systems are often difficult to install and diagnose, and offer no real-time system or level readout. Such features can be found on certain traditional systems, but can come with their own drawbacks. For example, solutions like bubblers, displacers, and capacitance transducers require complex setup and installation. Other more modern technologies such as ultrasonic, radar, and magnetostrictive floats can be prohibitively expensive.
The Solution
Modern hydrostatic systems offer many improvements in the aforementioned areas. Perhaps most notably is how incredibly simple they can be to install and program, which generally only requires placing the sensor in the bottom of the tank, calibrating, and adding whatever pump control or alarms are required. Furthermore, these are field reprogrammable at any time, or even remotely. Moreover, these solutions offer precise, digital readings of the current level and system state, both locally on a controller display and aggregated in a remote location for monitoring. Hydrostatic systems are incredibly cost-effective as well, very compact, and useful for irregularly shaped or even naturally-occurring vessels. Finally, they offer a robust reading, uninfluenced by many external factors such as mineral content, viscosity, or other possible contaminants.
How It Works
Figure 1: Diagram of a possible liquid level sensing installation utilizing a pressure-sensitive diaphragm and hall sensor to measure and compare fluid pressure to atmospheric pressure.
Hydrostatic liquid level sensing relies on the pressure exerted on a sensor by the column of water directly above the sensor, which is directly proportional to the volume of water in the tank. Pressure is measured by electromagnetically measuring the displacement of a diaphragm at the bottom of the tank [1].
Recent Innovations
Progress has been made to further refine this technology even in the last few years. Specifically, new technologies have allowed such sensors to become even more sensitive, and significantly less impacted by the effects of temperature [2]. Furthermore, certain transducers can provide simple solutions even for sanitary conditions like food and beverage, and can even be programmed to work with non-linear tanks [3].
Important Considerations
It is important to note that no solution is perfect for all applications. For example, digital systems will generally require separate hardware for switching high-current devices like pumps, due to the use of solid-state relays. Additionally, due to the nature of hydrostatic sensing measuring the pressure differential between the tank and ambient air, they are not suitable for pressurized vessels. Applications in freezing conditions, as well, are generally not suitable; however, this is also the case with many other technologies.
Conclusion
Unfortunately, there is no single perfect solution for all liquid level sensing applications; however, hopefully this blog post helped illustrate that hydrostatic sensing can be an excellent, simple, robust, and cost-effective solution for a wide variety of applications.
References
- F. Ali and N. Mandal, “Design and development of an electronic level transmitter based on hydrostatic principle,” Design and development of an electronic level transmitter based on hydrostatic principle, vol. 132, pp. 125–134, Sep. 2018.
- Vorathin, Z. M. Hafizi, and A. M. Aizzuddin, “A Novel Temperature-Insensitive Hydrostatic Liquid-Level Sensor Using Chirped FBG,” IEEE Sensors Journal, vol. 19, no. 1, pp. 157–162, Oct. 2018.
- Welander, “Hydrostatic liquid level sensor suited for sanitary and wash-down environments,” Control Engineering, Sep. 2010.